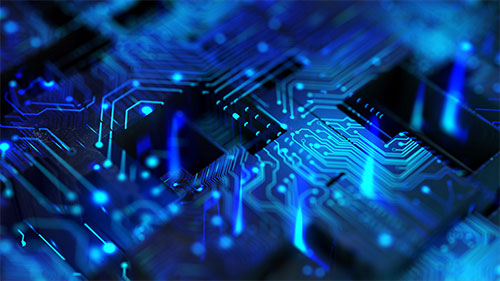
Process Optimization
Automation and AI can optimize various fabrication processes, leading to improved yield and reduced waste. AI algorithms can analyze vast amounts of data to identify patterns, anomalies, and potential areas for optimization, ensuring the production of high-quality semiconductor devices.
Quality Control
AI-based image recognition and machine learning algorithms can enhance quality control processes by quickly and accurately identifying defects or irregularities in semiconductor wafers. This ensures that only high-quality products reach the market.
Robotics in Manufacturing
Automated robotic systems are utilized in various stages of semiconductor manufacturing, such as wafer handling, material transportation, and assembly. Robotics enhance precision and speed, leading to higher production output and consistency.
Customization and Flexibility
Automation and AI technologies provide the flexibility needed for the semiconductor industry to adapt quickly to changing market demands. Production lines can be reconfigured more easily to accommodate different chip designs and specifications.
Research and Development
AI algorithms can assist in the design and optimization of semiconductor devices. From materials research to circuit design, AI can help engineers explore innovative solutions and accelerate the development of new technologies.
Predictive Maintenance
AI-powered predictive maintenance systems can monitor equipment health by analyzing data from sensors and other sources. This helps in identifying potential issues before they cause equipment failures, reducing downtime and maintenance costs.
Supply Chain Management
Automation and AI technologies can optimize supply chain operations, helping semiconductor manufacturers manage inventory efficiently, predict demand, and reduce lead times. This contributes to a more streamlined and responsive production process.
Advanced Data Analytics
AI enables advanced data analytics, allowing manufacturers to extract valuable insights from the massive amounts of data generated during the semiconductor fabrication process. This can lead to better decision-making, improved process control, and faster innovation.
Energy Efficiency
Automation and AI contribute to energy efficiency by optimizing the use of resources such as power and water. Smart systems can adjust energy consumption based on real-time production demands, reducing overall environmental impact.
Human-Machine Collaboration
Automation and AI technologies enable collaborative workflows where humans work alongside machines. This synergistic approach enhances overall productivity and leverages the strengths of both humans and machines.
Extreme Ultraviolet Lithography (EUVL)
EUVL is a cutting-edge technology used in semiconductor manufacturing for lithography. It utilizes extreme ultraviolet light with a wavelength in the nanometer range to create smaller features on semiconductor wafers. This technology allows for more precise and dense chip designs.
Quantum Dots
Quantum dots, which are semiconductor nanoparticles, are being researched for their potential in various applications, including in displays and photovoltaics. In the context of semiconductor fabrication, quantum dots can offer unique electronic and optical properties at the nanoscale.
Nanoscale Memory Technologies
Developments in non-volatile memory technologies at the nanoscale, including resistive switching memory (RRAM) and phase-change memory (PCM), are being explored for their potential in next-generation memory devices.
Nanowires and Nanotubes
Nanowires and nanotubes are structures with diameters in the nanometer range. They are being studied for their potential use in transistors, interconnects, and other components of semiconductor devices to improve performance and miniaturization.
Nanoscale Transistors
Continued advancements in transistor technology involve designing and manufacturing transistors at the nanoscale. Techniques such as FinFET (fin field-effect transistor) and gate-all-around (GAA) transistor structures have been explored to enhance performance and energy efficiency.
2D Materials and Nanosheets
Two-dimensional (2D) materials, such as graphene and transition metal dichalcogenides (TMDs), are being explored for their unique electrical and thermal properties. Researchers are investigating their integration into semiconductor devices to enhance performance.
Nanophotonics
Nanophotonics involves the use of nanoscale structures to manipulate and control light. In semiconductor fabrication, this can lead to advancements in on-chip communication, optical interconnects, and the development of nanoscale photonic devices.
Directed Self-Assembly (DSA):
DSA is a nanomanufacturing technique that uses self-assembly principles to guide the arrangement of nanoscale structures. This technique is explored for creating well-defined patterns at smaller scales in semiconductor manufacturing.
Signal Representation
Analog : Represents signals as continuous, varying voltages. Analog circuits process signals in a smooth and continuous manner.
Digital : Represents signals as discrete values (0s and 1s). Digital circuits process information in discrete steps.
Circuit Complexity
Analog : Typically involves simpler circuit designs and components, such as amplifiers, filters, and oscillators.
Digital : Often requires more complex circuitry, including logic gates, flip-flops, and memory cells.
Tolerance to Variability
Analog : More sensitive to variations in manufacturing processes and environmental conditions due to the continuous nature of signals.
Digital : Tends to be more robust in the face of manufacturing variations, allowing for greater tolerance.
Precision and Accuracy
Analog : Requires high precision and accuracy in manufacturing to maintain signal integrity and minimize noise.
Digital : Can tolerate some level of imprecision, and error correction techniques can be applied.
Power Consumption
Analog : Often consumes less power for specific applications, as it can process signals with less computational overhead.
Digital : May consume more power, especially in applications with high computational demands.
Applications
Analog : Commonly used in applications where signals need to be processed in a continuous manner, such as audio amplifiers, analog sensors, and radio frequency circuits.
Digital : Widely used in applications involving data processing, communication, computation, and storage, such as microprocessors and memory devices.
Manufacturing Complexity
Analog : Fabrication processes may involve specific analog design techniques and may require special attention to layout and matching.
Digital : Involves the fabrication of complex integrated circuits with intricate designs, including logic gates and memory cells.
Testing and Verification
Analog : Testing often involves measuring electrical characteristics and ensuring that the circuit meets specifications across a range of operating conditions..
Digital : Verification often involves functional testing and ensuring that the circuit performs logical operations accurately.
Design Flexibility
Analog : Designers have more freedom to optimize for specific performance criteria but may face challenges in achieving consistency.
Digital : Designers often work with standardized components and logic gates, allowing for better predictability and scalability.
Cost
Analog : Fabrication costs can be lower for simpler circuits, but specialized processes may increase costs for certain applications..
Digital : Costs can be higher due to the complexity of digital circuits, but economies of scale often apply.
Advanced Nodes and FinFET Technology
Continued advancements in scaling down semiconductor technology to smaller nodes, including the widespread adoption of FinFET (fin field-effect transistor) and other 3D transistor structures.
Extreme Ultraviolet Lithography (EUVL)
Increased implementation of EUVL for photolithography in semiconductor manufacturing, allowing for the production of smaller and more densely packed features on wafers.
5G Technology and RF Semiconductor Integration
Growing demand for semiconductor solutions to support 5G technology, including the integration of radio-frequency (RF) components into semiconductor devices.
Advanced Memory Technologies
Development and adoption of advanced memory technologies such as DDR5, HBM (High Bandwidth Memory), and persistent memory solutions for improved performance and energy efficiency.
Quantum Computing and Quantum Dot Technologies
Explorations into the potential of quantum computing technologies and the use of quantum dots in semiconductor devices for unique electronic and optical properties.
3D NAND Flash Memory
Widespread adoption of 3D NAND flash memory technology for increased storage density and improved performance in memory devices.
Silicon Carbide (SiC) and Gallium Nitride (GaN) Power Devices
Growing interest in wide-bandgap materials such as SiC and GaN for power semiconductor devices, enabling higher efficiency and power density.
More-than-Moore (MtM) Technologies
Increasing focus on MtM technologies beyond traditional Moore’s Law scaling, including heterogeneous integration, advanced packaging, and system-level innovations.
AI Hardware Accelerators
Development of specialized hardware accelerators, including AI-specific chips and neuromorphic computing devices, to support the increasing demand for artificial intelligence applications.
Advanced Packaging and System-in-Package (SiP)
Innovation in packaging technologies, such as advanced interconnects, 2.5D and 3D stacking, and SiP architectures to enhance performance and integration.
In-Memory Computing
Exploration of in-memory computing architectures, which process and store data in the same location, for improved computational efficiency and reduced data movement.
Edge Computing and IoT Devices
Semiconductor technologies designed to meet the requirements of edge computing and Internet of Things (IoT) devices, including low-power and energy-efficient solutions.
Environmental Sustainability Practices
Increasing emphasis on sustainability practices in semiconductor fabrication, including energy-efficient manufacturing processes, waste reduction, and eco-friendly materials.
Photonic Integration
Integration of photonic components on semiconductor chips for improved data communication and processing speed.
Biomedical and Bioelectronic Devices
Exploration of semiconductor technologies for applications in biomedical devices, bioelectronics, and implantable sensors.
Online Learning Platforms
Platforms like Coursera, edX, and Udacity offer courses on semiconductor technology. Look for courses from reputable institutions or industry experts that cover topics such as semiconductor physics, device fabrication, and cleanroom practices.
Industry Training Programs
Some semiconductor companies offer training programs for new hires or individuals interested in entering the industry. Check with major semiconductor manufacturers or foundries for information on their training initiatives.
Professional Organizations
Join professional organizations related to semiconductor technology, such as the IEEE Electron Devices Society. These organizations may provide resources, conferences, and networking opportunities that can enhance your knowledge and skills.
Vendor-Specific Training
Some semiconductor equipment and technology vendors offer training programs on the use of specific tools and processes. This can be beneficial if you want to specialize in a particular aspect of semiconductor fabrication.
Electronics and Consumer Goods
Integrated circuits (ICs), microcontrollers, and microprocessors are used in consumer electronics such as smartphones, tablets, laptops, TVs, and smartwatches.
Telecommunications
Semiconductors are fundamental in telecommunications for signal processing, data transmission, and networking. They are used in devices like routers, modems, and base stations.
Automotive Industry
Semiconductor devices are essential in modern vehicles for engine control units (ECUs), safety systems, entertainment systems, navigation, and advanced driver-assistance systems (ADAS).
Healthcare
Medical devices rely on semiconductors for applications like imaging equipment (MRI, CT scans), patient monitoring systems, diagnostic equipment, and implantable medical devices.
Aerospace and Defense
Semiconductors are used in avionics, radar systems, navigation equipment, communication systems, and defense electronics for various aerospace and defense applications.
Industrial Automation
Programmable logic controllers (PLCs) and microcontrollers in industrial automation systems facilitate control and monitoring of machinery, manufacturing processes, and robotics.
Energy Sector
Power electronics, including semiconductor devices such as thyristors and power transistors, are used in power generation, distribution, and renewable energy systems.
Information Technology (IT)
Servers, data storage devices, networking equipment, and data centers rely heavily on semiconductor technology to process, store, and transmit information.
Renewable Energy
Semiconductor devices are used in solar inverters and wind turbine control systems to convert and manage electrical power generated from renewable sources.
Smart Grids
Semiconductors contribute to the development of smart grids, enabling efficient monitoring, control, and communication within electrical grids.
Consumer Appliances
Semiconductors are used in a variety of home appliances such as refrigerators, washing machines, air conditioners, and microwave ovens for control and automation.
Internet of Things (IoT)
IoT devices, including sensors, actuators, and communication modules, heavily rely on semiconductor technology to enable connectivity and smart functionality.
Entertainment and Gaming
Semiconductor devices power gaming consoles, graphics cards, audio processors, and other entertainment systems.
Financial Services
Semiconductor devices are used in servers and systems that facilitate financial transactions, secure communications, and data processing in the financial industry.
Environmental Monitoring
Semiconductors play a role in sensors used for environmental monitoring, including air quality sensors, temperature sensors, and water quality sensors.
Particle Control
Cleanrooms are designed to minimize airborne particles, including dust, dirt, and microorganisms. Even small particles can negatively impact the quality and functionality of semiconductor devices. The cleanroom environment helps prevent contamination during the manufacturing process.
Temperature and Humidity Control
Semiconductor fabrication processes often require precise control of temperature and humidity. Fluctuations in these parameters can affect the performance and reliability of semiconductor devices. Cleanrooms provide a stable and controlled environment to ensure consistent manufacturing conditions.
Air Quality and Ventilation
Cleanrooms use high-efficiency air filtration systems to maintain a controlled level of air cleanliness. The air is typically recirculated and filtered to remove particles. Ventilation systems are designed to ensure the proper exchange of air, preventing the buildup of contaminants.
Worker Hygiene
Personnel entering cleanrooms must adhere to strict protocols to maintain cleanliness. This includes wearing specialized cleanroom garments, such as coveralls, gloves, masks, and hairnets, to minimize the introduction of contaminants.
Equipment and Tool Control
Cleanroom equipment and tools used in semiconductor fabrication are specially designed to minimize particle generation. Regular maintenance and cleaning procedures are implemented to prevent equipment-related contamination.
Preventing Chemical Contamination
Cleanrooms help control chemical contamination by limiting the use of volatile chemicals and ensuring that any chemicals used in the fabrication process are carefully monitored and controlled.
Stringent Cleanroom Classes
Cleanrooms are classified based on the maximum allowable number of particles per cubic meter. The International Organization for Standardization (ISO) defines cleanroom classes, with Class 1 being the cleanest. Semiconductor fabrication typically requires cleanrooms with stringent cleanliness levels, often in the ISO 3 to ISO 7 range.
Stringent Standards and Regulations
Semiconductor manufacturing is subject to strict industry standards and regulations to ensure the quality and reliability of the produced devices. Cleanroom facilities help meet and maintain compliance with these standards.
Quality and Yield Improvement
By maintaining a clean and controlled environment, cleanrooms contribute to higher manufacturing yields and improved product quality. The reduction of defects and contaminants leads to better-performing semiconductor devices.
Specialized Cleanroom Areas
Different stages of semiconductor fabrication may require different cleanliness levels. Cleanroom facilities are often segmented into specialized areas for specific manufacturing processes, each with its cleanliness requirements.
Wafer Inspection
Quality control engineers may be involved in inspecting semiconductor wafers for defects, irregularities, or contamination. This involves using advanced inspection tools and techniques to ensure the integrity of the wafer before subsequent processing steps.
Metrology and Measurement
Quality control engineers are responsible for measuring and verifying critical dimensions, layer thicknesses, and other parameters during the semiconductor manufacturing process. This involves using metrology tools to ensure that the fabricated devices meet precise specifications.
Cleanroom Protocol Compliance
Ensuring compliance with cleanroom protocols is vital for quality control. Engineers monitor and enforce adherence to cleanroom procedures and practices to minimize contamination risks during fabrication.
Defect Analysis and Root Cause Investigation
Quality control professionals investigate defects in semiconductor devices, analyzing root causes and implementing corrective actions. This process helps improve overall manufacturing quality and prevent the recurrence of issues.
Process Control and Monitoring
Quality control engineers monitor and control various processes within the fab to ensure consistency and adherence to specifications. This involves implementing statistical process control (SPC) techniques and making real-time adjustments to maintain quality.
Automated Test Equipment (ATE) Operation
In semiconductor fabs, testers operate and maintain automated test equipment to evaluate the electrical performance of semiconductor devices. They may develop test programs and conduct extensive testing to ensure functionality and reliability.
Reliability Testing
Quality control engineers conduct reliability testing to assess the long-term performance and durability of semiconductor devices. This includes accelerated life testing, thermal cycling, and other tests to simulate real-world conditions.
Quality Assurance Systems Implementation
Implementing and managing quality assurance systems within the fab, including ISO standards and other quality management frameworks, to ensure that the manufacturing processes adhere to global quality standards.
Supplier Quality Management
Collaborating with suppliers to ensure the quality of materials and components used in semiconductor fabrication. This involves establishing quality control processes for incoming materials.
2D Semiconductor Manufacturing
Established Technology
2D semiconductor manufacturing has been the traditional approach and is well-established in the industry. Many semiconductor fabs currently use 2D processes.
Skill Utilization
If you have a strong background in 2D semiconductor manufacturing processes, there are still abundant opportunities in optimizing and refining these processes for improved performance and efficiency.
Legacy Systems
Some applications and industries continue to rely on 2D semiconductor devices. Legacy systems and devices may require ongoing support and improvements.
Specialization
Specializing in 2D semiconductor manufacturing can make you valuable in industries that haven’t fully transitioned to 3D technologies.
3D Semiconductor Manufacturing
Emerging Technology
3D semiconductor manufacturing represents the next frontier in chip design and offers opportunities to work on cutting-edge technologies.
Vertical Integration
3D manufacturing involves stacking multiple layers of components, enabling increased performance and reduced footprint. This requires a multidisciplinary approach and understanding of vertical integration.
Innovative Solutions
Working in 3D semiconductor manufacturing allows you to contribute to innovative solutions for overcoming the limitations of 2D technology, such as improved power efficiency and performance.
Future Growth
Many experts consider 3D technology as the future of semiconductor manufacturing. Choosing this path may position you at the forefront of industry trends and advancements.
Diverse Opportunities
3D technology opens up opportunities beyond traditional semiconductor fabrication, including applications in packaging, memory devices, and advanced computing.
Recommendations
Industry Trends
Research current industry trends and projections to understand the direction of semiconductor manufacturing. Identify areas of growth and demand.
Skill Development
Assess your skills and interests. If you enjoy working on cutting-edge technologies and have a strong foundation in multidimensional designs, 3D semiconductor manufacturing may be a natural fit.
Continuous Learning
Semiconductor technology evolves rapidly. Consider continuous learning and staying updated on the latest advancements to remain competitive in the job market.